computer numerical control (CNC)
What is computer numerical control (CNC)?
Computer numerical control (CNC) is a manufacturing method that automates the control, movement and precision of machine tools through the use of preprogrammed computer software, which is embedded inside the tools.
CNC is commonly used in manufacturing for machining metal and plastic parts. Mills, lathes, routers, drills, grinders, water jets and lasers are common cutting tools whose operations can also be automated with CNC. It can also be used to control nonmachine tools, such as welding, electronic assembly and filament-winding machines.
How computer numerical control works
With CNC, each object to be manufactured gets a custom computer program, usually written in an international standard language called G-code, stored in and executed by the machine control unit (MCU), a microcomputer attached to the machine. The M-code language is also used in conjunction with G-code in CNC operations.
While G-code controls the movement and functioning of the machine, M-code controls the operation's external movements. The program also contains the instructions and parameters the machine tool follows, such as the feed rate of materials and the positioning and speed of the tool's components.
Early in the process, engineers create a computer-aided design (CAD) drawing of the part to be manufactured and then translate the drawing into G-code. The program is loaded onto the MCU, and a machine operator performs a test run without the raw material in place to ensure proper positioning and performance. This step is important because incorrect speed or positioning can damage both the machine and the part.
When everything is ready, the CNC machine runs its program and completes jobs with precision as instructed. The jobs could involve anything from creating something from scratch to cutting a workpiece or printing anything.
Why is computer numerical control important?
Numerical control enables machines to produce items more quickly and with better surface finishes without the need for manual machining or extensive human participation.
The following are some benefits of CNC systems:
- Cost reduction. CNC machines are cost-effective and bring down the cost of production due to precision manufacturing. Energy consumption is decreased as a result of increased production efficiency, scalability and less material waste, which also lowers operating expenses. The weight of potential financial obligations related to worker safety is also lessened, which helps with cost-cutting.
- Waste reduction. The software used to run various kinds of CNC machines results in little to no waste during the manufacturing process due to simulations and repeated optimizations.
- Improved worker safety. CNC machines minimize the chance of accidents and guarantee worker safety because there is less need for human interaction. Most modern CNC machines are self-sufficient and can be handled remotely by people for software upgrades, design changes or other preventative maintenance.
- Human error reduction. Since human error is eliminated in the manufacturing process with CNC, it is thought to offer greater precision, complexity, speed, flexibility and repeatability. This ultimately results in fewer defects in the manufactured products.
- Contour machining. CNC provides capabilities such as contour machining, which enables milling of contoured shapes, including those produced in 3D printing and designs.
- Faster MCU programming. Some CNC systems are integrated with CAD software and computer-aided manufacturing software, which can speed the process of programming the MCU.
- Improved operational intelligence. Integration with enterprise resource planning software and related applications, such as enterprise asset management software, can facilitate operational and business intelligence processes and help improve plant performance and maintenance.
- No bottlenecks. With the higher level of automation used, CNC systems reduce production and manufacturing bottlenecks and improve the outcome.
Along with the wonderful benefits that CNC machines offer, they do tend to be more expensive, require more maintenance than other production methods and compel companies to hire a skilled CNC programmer.
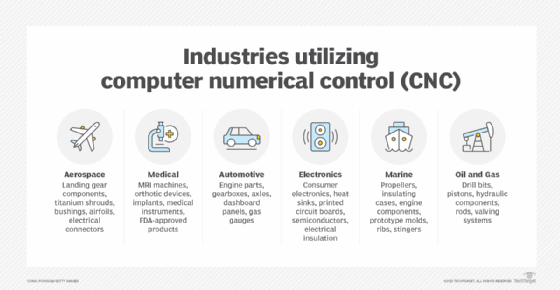
Computer numerical important applications
CNC plays an integral role in critical industries and sectors, such as medicine, aerospace, military and defense. Because a component's failure could endanger lives, businesses in these industries demand the highest level of precision in their parts, which CNC machines can offer.
The following are some industries that utilize CNC machinery.
Aerospace
The accuracy needed to manufacture every component of an airplane is increased by CNC. This includes everything from the outer shell to the innermost parts. The highest levels of precision and accuracy must be used when manufacturing CNC-machined aerospace components since they are often mission-critical. Also, there are frequently stringent requirements for flatness, roundness and cylindricity that can only be met with computer-aided machining, and tolerances as small as 0.00004 inches are not unusual.
Aluminum, stainless steel, brass, nickel, bronze, ceramics, plastics, magnesium, titanium and high-performance alloys, such as Inconel and Kovar, are a few of the materials that can be utilized in aerospace CNC machining.
A few examples of CNC-machined components are the following:
- Landing gear components.
- Titanium shrouds.
- Airfoils.
- Bushings.
- Stator assemblies.
- Manifolds.
- Magnesium gearbox housings.
- Electrical connectors.
Medical equipment
To meet patient needs, the medical industry primarily relies on specialized, accurate and high-quality products produced by CNC machinery. During the COVID-19 pandemic, when the need for medical products such as masks and respirators rose, this dependence on CNC machines increased. Disposable medical equipment is also often used to prevent people from contracting infectious diseases while receiving medical care. Because of this, it is even more crucial for the medical sector to employ CNC to increase and accelerate the production of medical products.
Typical examples of products made through CNC machines include the following:
- Magnetic resonance imaging machines.
- Implants.
- Orthotic devices.
- Electronic enclosures for monitoring devices.
- Research equipment.
- Shielded enclosures.
- Parts made from high-temperature plastics.
- Medical instruments.
- Customized sterile packaging.
- Food and Drug Administration-approved products.
Automotive
One of the key markets for CNC machining is the automotive industry. Every step of the automobile manufacturing industry, from prototyping in research and development to producing large quantities of parts, benefits from using CNC machining.
Furthermore, a wide range of components, including massive engine block sections and small gears and panels, are produced by CNC milling machines and lathe equipment. For a combustion engine alone, several CNC machines are needed. These can be used for converting massive metal blocks into engine body panels and producing the cylinders, pistons and other components that go into making the cylinder assembly in the engine block.
Some of the components made through CNC machining are the following:
- Gearboxes.
- Engine parts.
- Axles.
- Valves.
- Dashboard panels.
- Cylinder blocks.
- Gas gauges.
Electronics
CNC machining is a useful manufacturing method for the electronics sector because of its accuracy and adaptability. Both conductive and nonconductive metals, as well as a variety of polymers, can be processed by CNC machines. With CNC technology, there is no need for a preproduction tooling stage, which speeds up the production of electronic components. Designs can also be easily modified and iterated with minimal supervision. Apple reportedly has 10,000 CNC machines and manufactures CNC-machined laptops on a massive scale.
Some examples of items produced by CNC machinery are the following:
- Consumer electronics.
- Semiconductors.
- Heat sinks.
- Printed circuit boards.
- Electrical insulation.
- Amplifier housings.
- Radio frequency interference shieldings.
Oil and gas
Large machinery used in drilling rigs and refineries is designed with CNC machines to ensure a flawless fit. An imperfect fit can cause cylinders to not fill, pistons to not exert the proper amount of pressure and valves to leak. Therefore, to ensure that the parts fit precisely as required, petrochemical businesses utilize parts that have been CNC-machined.
A few examples of parts created through CNC machines are the following:
- Drill bits.
- Rods.
- Pistons.
- Valves.
- Hydraulic components.
- Valving systems.
Marine
Because highly precise parts are required to keep ships running and afloat, the marine industry heavily relies on CNC machines. Watercraft require a plethora of equipment, including underwater sensors and communication equipment. As a result, the marine industry must use CNC precision when manufacturing boats and other marine equipment.
Some common parts manufactured through CNC machines are the following:
- Propellers.
- Insulating cases.
- Components for the engine.
- Prototype molds.
- Ribs.
- Stingers.
History of computer numerical control
Over the last several decades, CNC technology has progressed from punch tape-controlled devices to machines that accept CNC programming input and produce 3D machine parts with extreme precision.
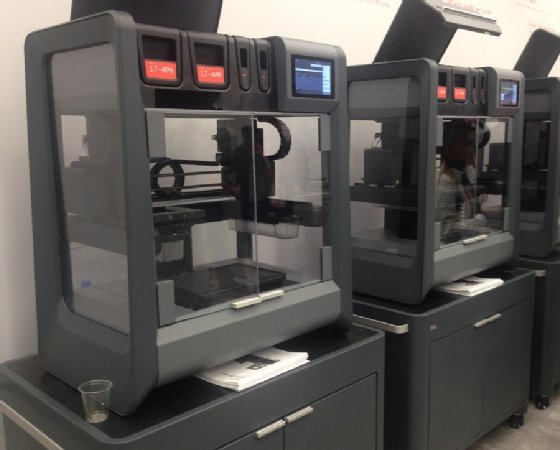
The origins of CNC machines can be traced back to John Parsons. He is credited with creating the first numerical control machine in 1949, which was designed to run directly off a set of punch cards that told the machine where to move. The Cincinnati Milacron Hydrotel, the first commercially available CNC machine, was later introduced in 1952 by a team of Massachusetts Institute of Technology researchers.
CNC machines were first patented in 1958.
The processes of additive and subtractive manufacturing are distinct yet connected at the same time. Discover the key distinctions between these two manufacturing approaches.